Details
4-DOF High-Torque Serial Bus Servo Robotic Arm
Supports flexible expansion and secondary development


RoArm-M2 series is a 4DOF smart robotic arm designed for innovative applications. Adopts lightweight structure design with a total weight of less than 900g and the effective payload of [email protected], it can be flexibly mounted on various mobile platforms. Adopts a 360°omnidirectional base combined with three flexible joints to create a workspace with a 1-meter diameter.
The joint direct-drive design enhances repositioning precision and also improves structural reliability, with innovative dual-drive technology doubling the shoulder joint torque. Onboard ESP32 MCU main control module supports multiple wireless control modes, provides control interfaces and rich communication protocols for easily connecting to various devices.
Provides a user-friendly and cross-platform WEB application that integrates a simple and visualized coordinate control mode, making it easier to get started. Comes with rich graphic and video tutorials to help you learn and use it quickly. Compatible with ROS2 and various host computers, supports various wireless and wired communication modes. Comes with an expansion plate, supports customizing the EoAT (End of Arm Tooling) to meet innovative application requirements.
RoArm-M2 series achieves an excellent balance between lightweight, user-friendliness, expandability, and open innovation, it is a multifunctional robotic arm that integrates intelligent control, human-machine interaction, and customizable development. Ideal for applications that require a combination of flexibility, expandability, and user-friendliness.
Provides options for RoArm-M2-S / RoArm-M2-Pro. The upgraded version RoArm-M2-Pro is equipped with all-metal ST3235 bus servos, offering a more rugged body and stable backlash that won't increase with use, enhancing product durability.

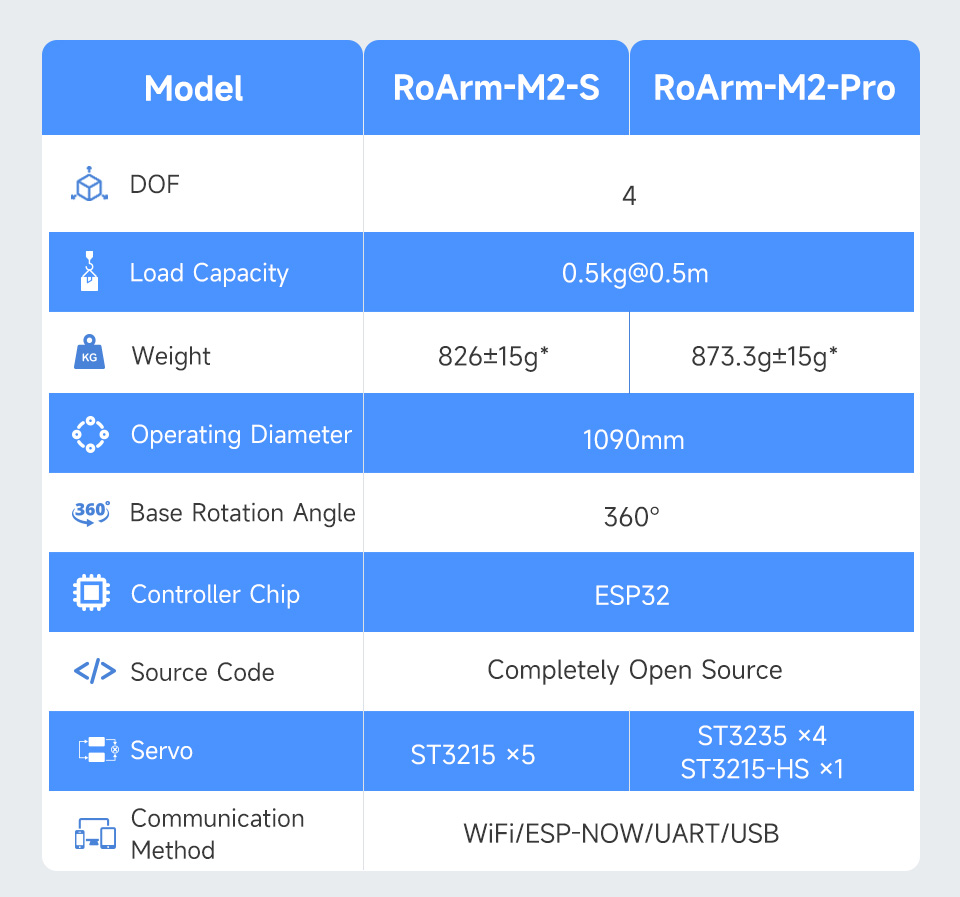
* Not including the weight of the table edge fixing clamp (290g).

The EoAT supports various mounting methods, can be used as a clamp or as the fourth degree of freedom. Provides Open-source DXF and 3D models for DIY and secondary development
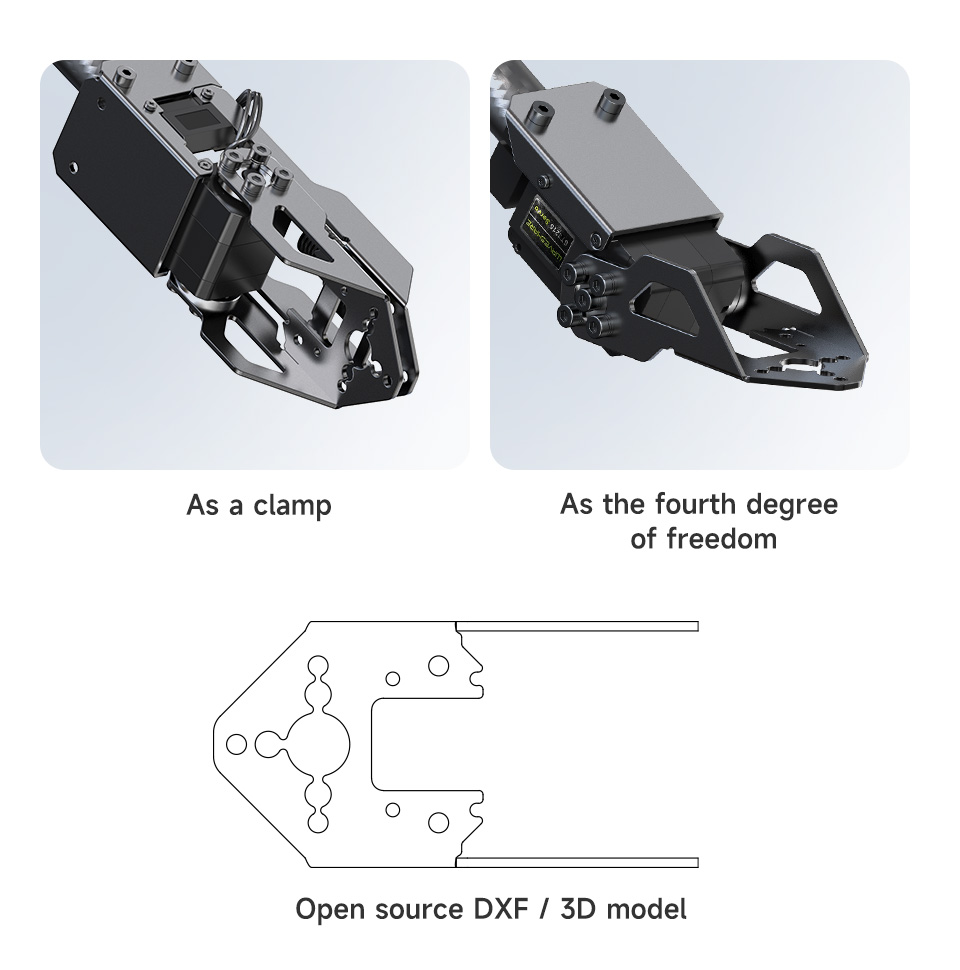

Adopts 360° rotation base and flexible joints to create an omnidirectional operating space with a 1-meter diameter, allowing the EoAT to move freely in all directions
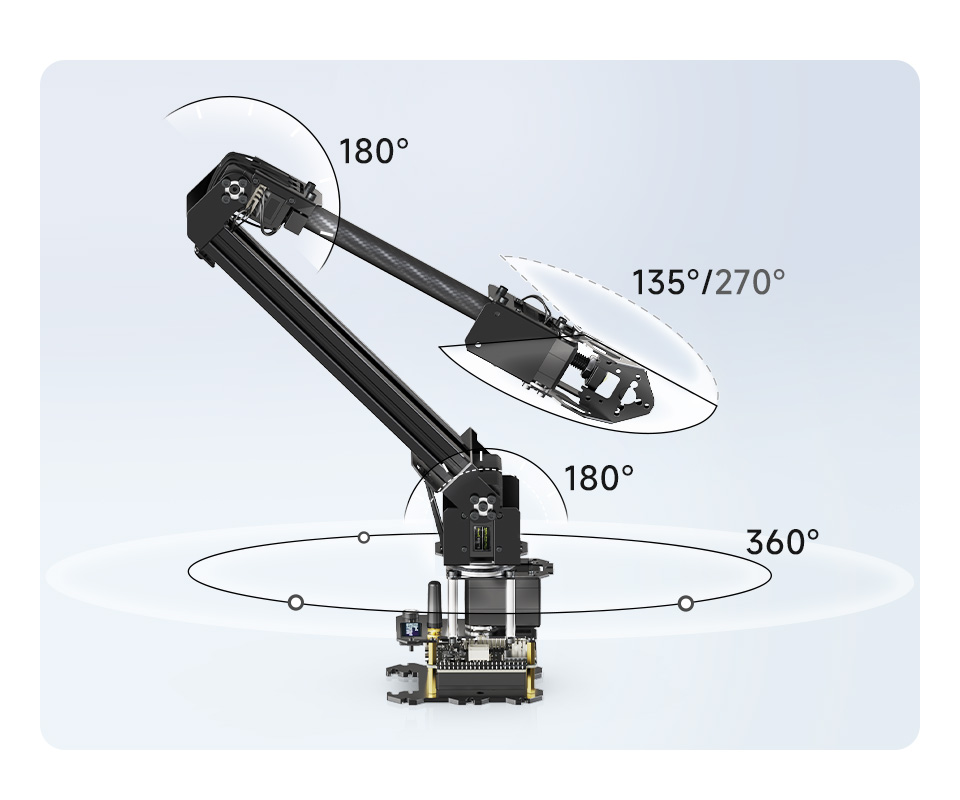
Cross-platform Web Application

No App installation required, access after entering the address. Allows users to connect and control RoArm-M2 via mobile phones, tablets and computers by clicking the buttons on the Web App. Supports secondary development of this open-source Web App to customize the user interface and add new functions.
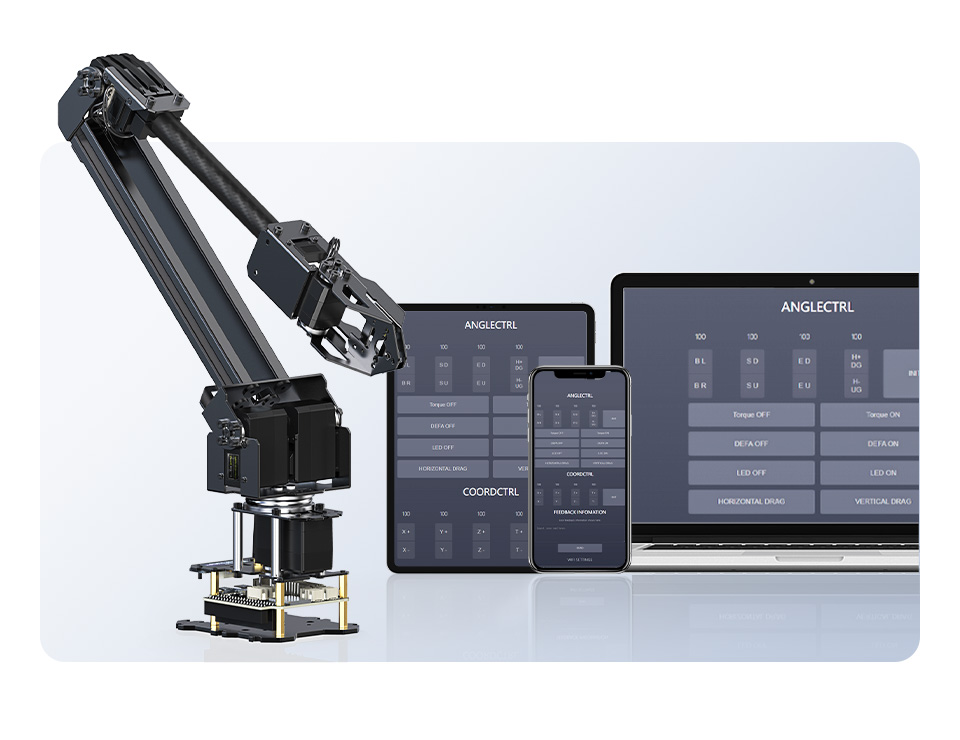
secondary development

Completely open source for the control codes and communication interface documents of Roarm-M2 series, supports multiple languages and devices for secondary development. Provides modularized demos and tutorials for zero-based users, easy to get started.
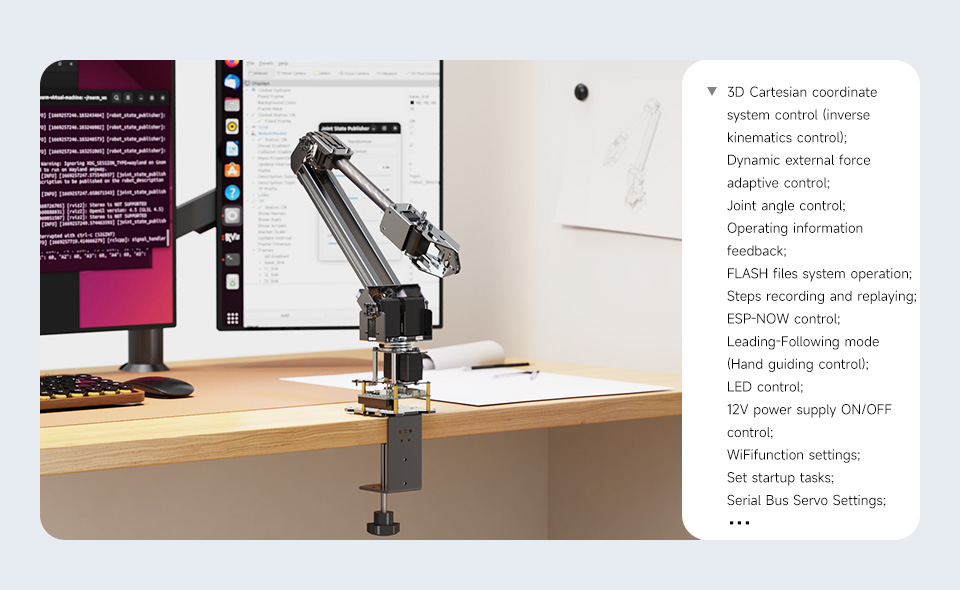

lightweight body with a total weight of less than 900g, adopts carbon fiber
and 5052 aluminum alloy to ensure stability under heavy loads,
suitable for various mobile robot chassis
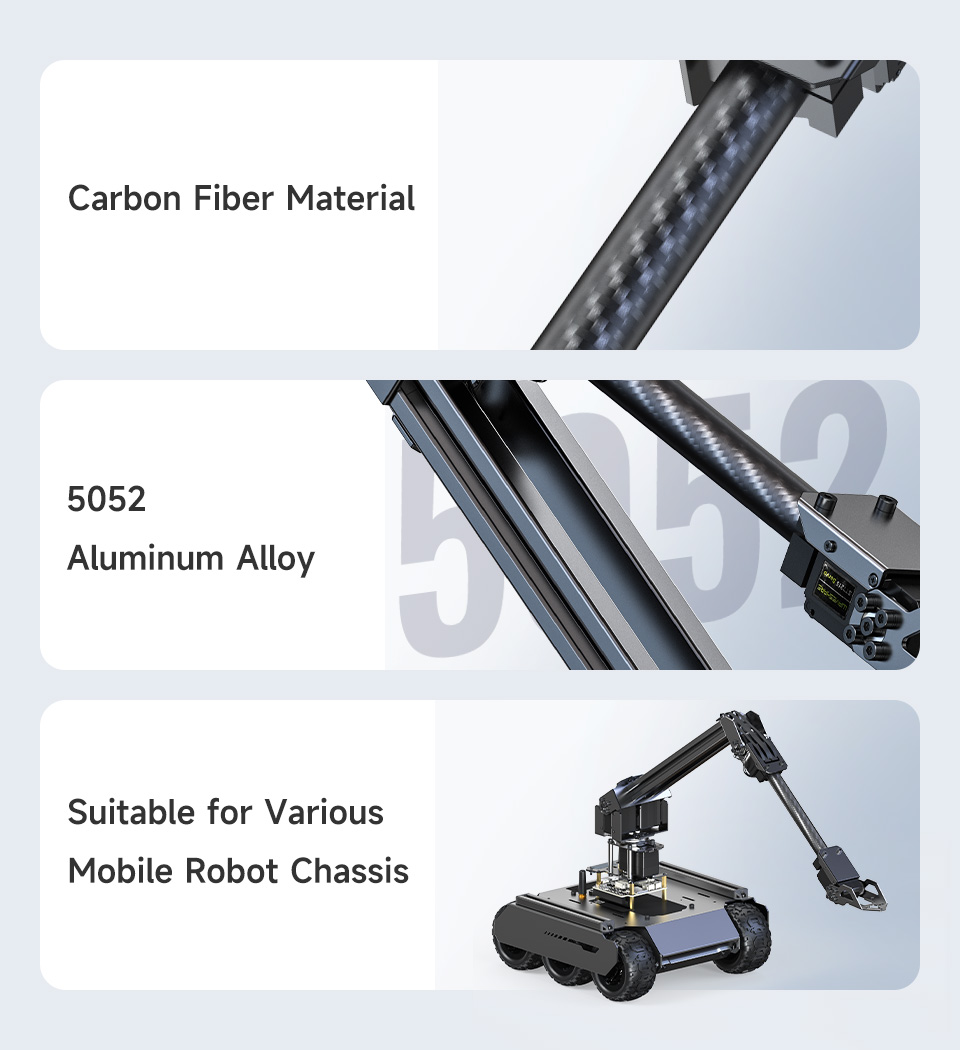
The Feedback precision up to 0.088°

The joint angle feedback can be obtained directly via a 12-bit high-precision magnetic encoder without any reduction groups, which is more accurate, and the actual position of the current target point can be calculated based on the joint angle feedback.
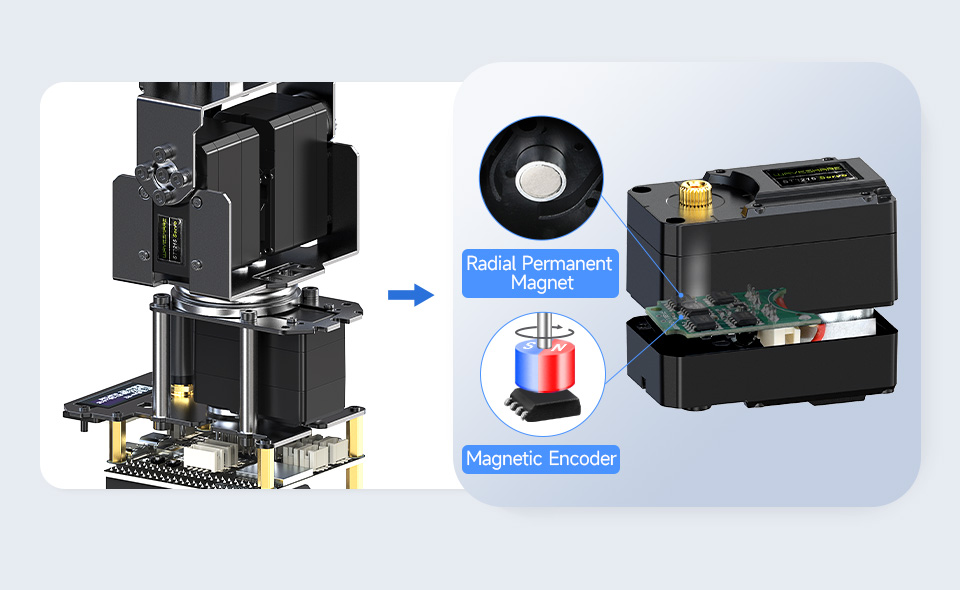
doubles the shoulder joint torque

We have developed a dual-drive control algorithm that allows the two servos at the shoulder joint to coordinate their output torque effectively, significantly enhancing
the power and the overall load capacity of RoArm-M2 Series
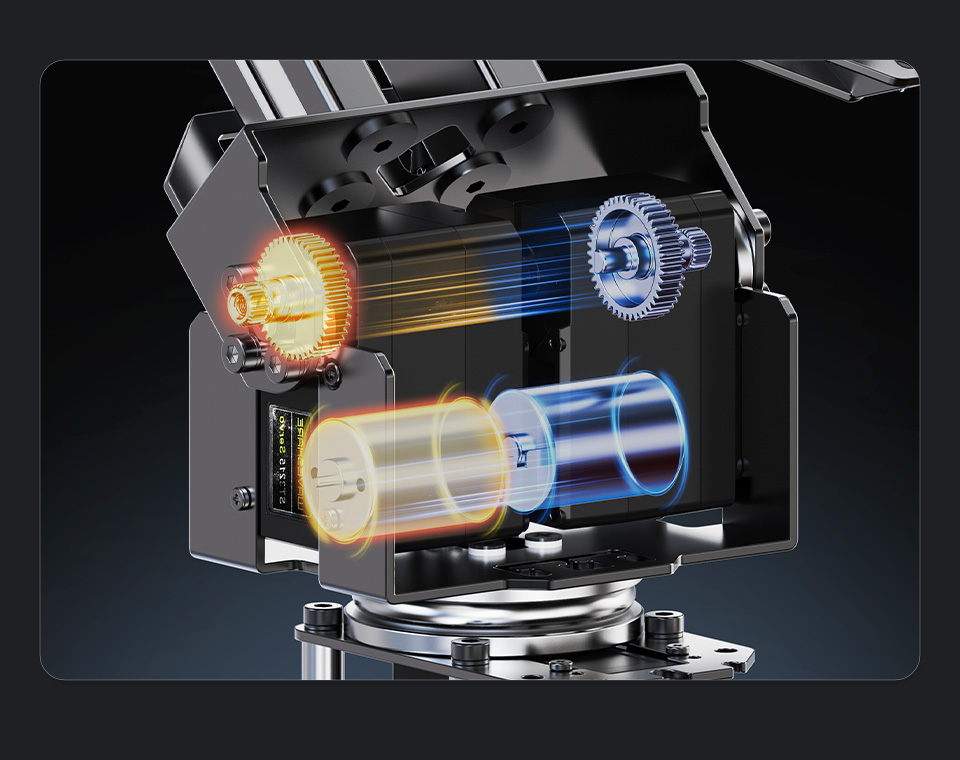
force control

The direct-drive clamp design allows precise control of the clamp force in the program, suitable for clamping delicate objects without applying excessive force
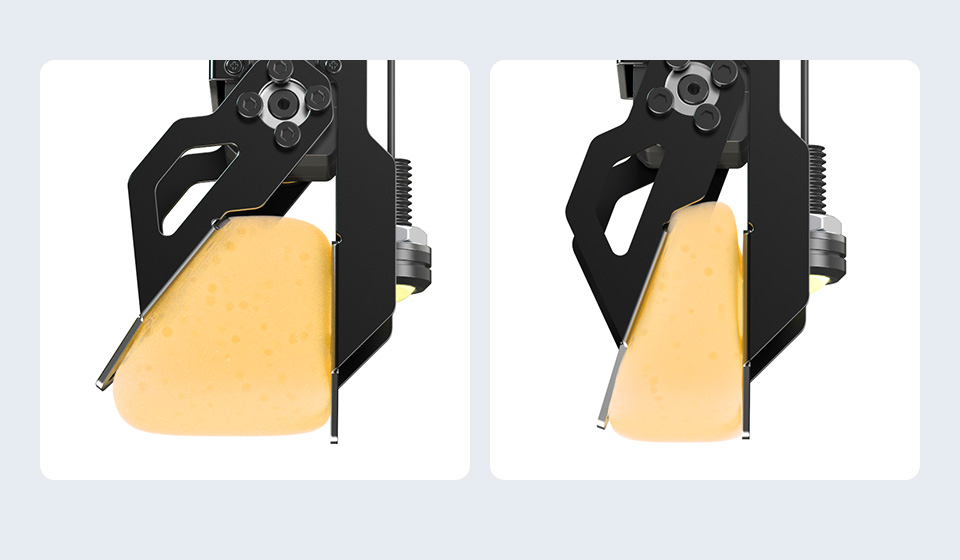
to compensate for the influence
of gravity

The SHOULDER and ELBOW joints support installing the rubber bands to assist the robotic arm, by utilizing the elastic contraction of rubber bands to compensate for the influence of gravity and increase the effective load of the robotic arm.
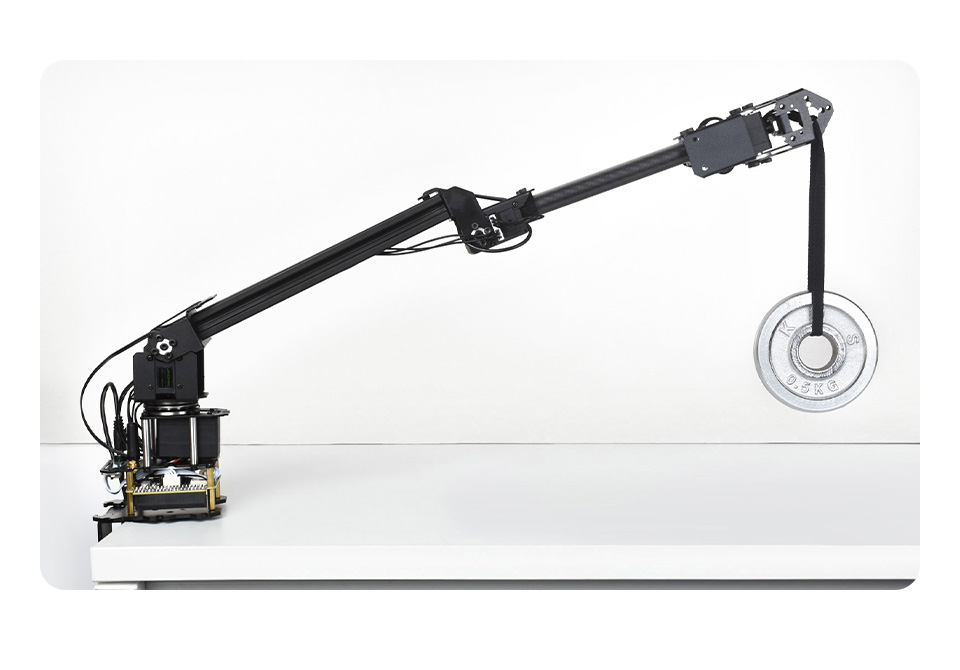
adaptive control

After enabling this function, you can limit the maximum torque for each joint. When the external force applied to the joint exceeds the torque threshold (configurable), the robotic arm will rotate in response to the external force, and will return to the specified position when the external force decreases below the torque threshold.
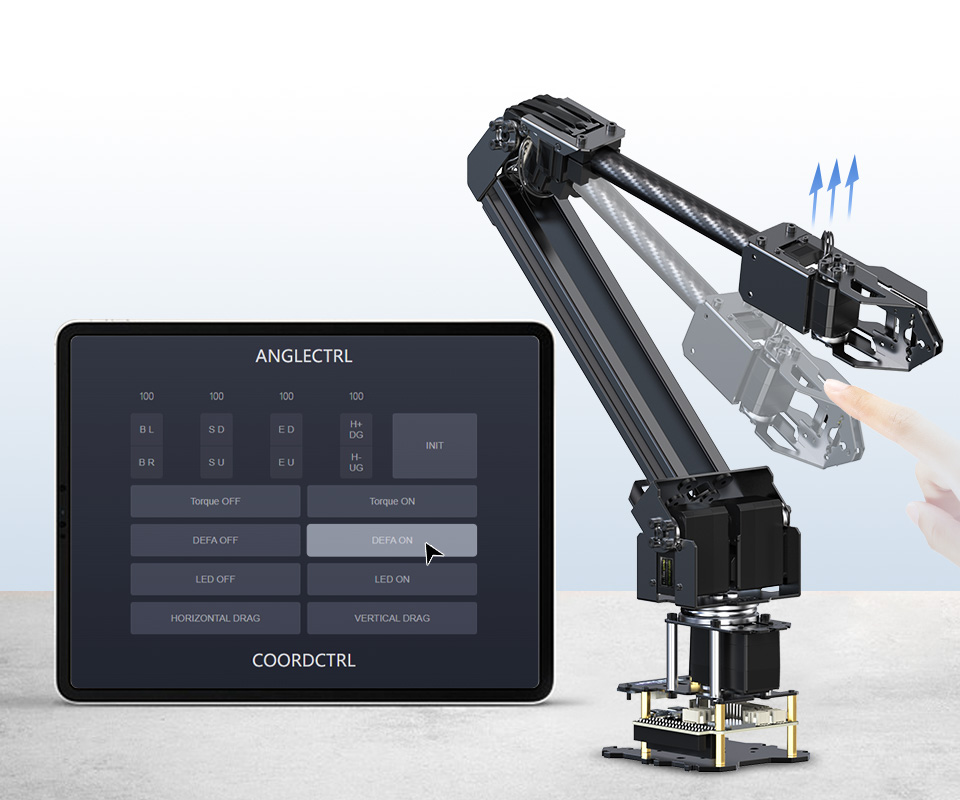
Easy to create actions

RoArm-M2 can save JSON instructions for robot control as task files. The task files can be saved in the Flash of ESP32, which will not be lost in case of power loss. The robotic arm can perform complex and repetitive operations by calling these task files.
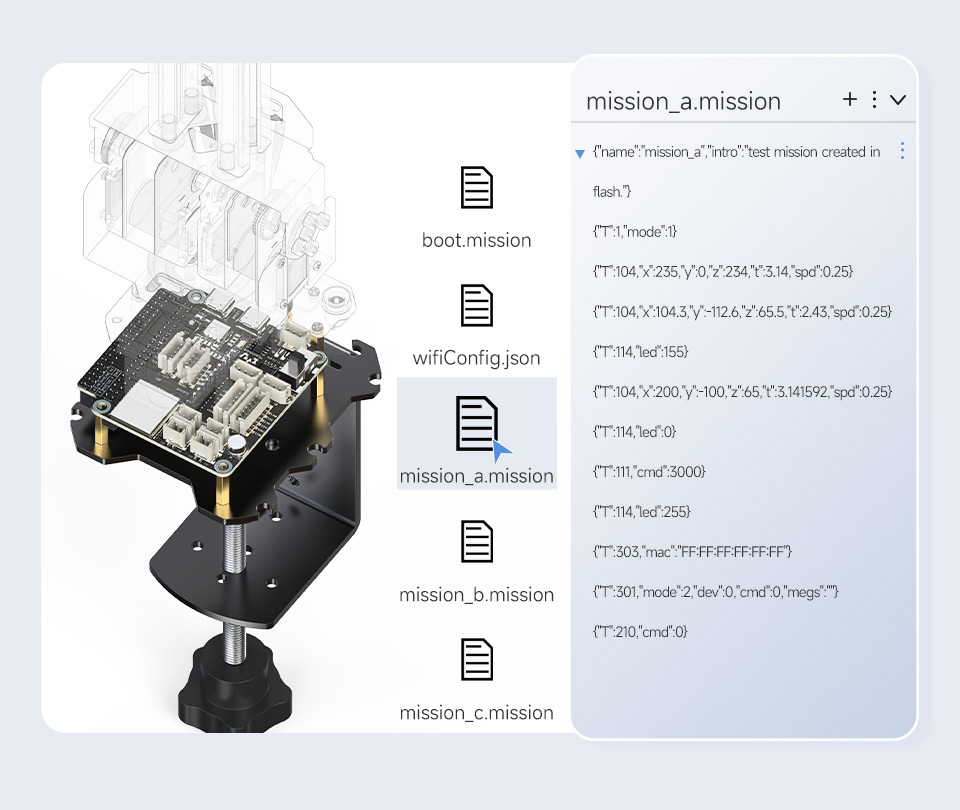

Open source for inverse kinematics control algorithm in the three-dimensional Cartesian coordinate system. After entering the target position, the robot arm can accurately reach the target point by using the inverse kinematics function to calculate the rotation angle of each joint.
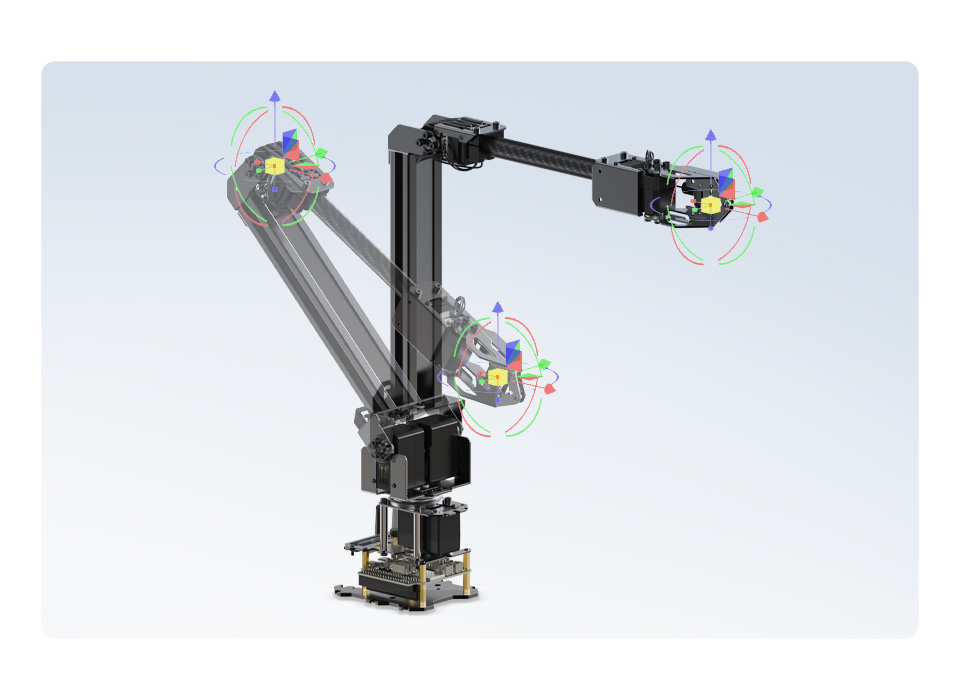
Smoother movement

We use the curve velocity control algorithm to make the robotic arm move smoother and more naturally, without oscillations during start and stop
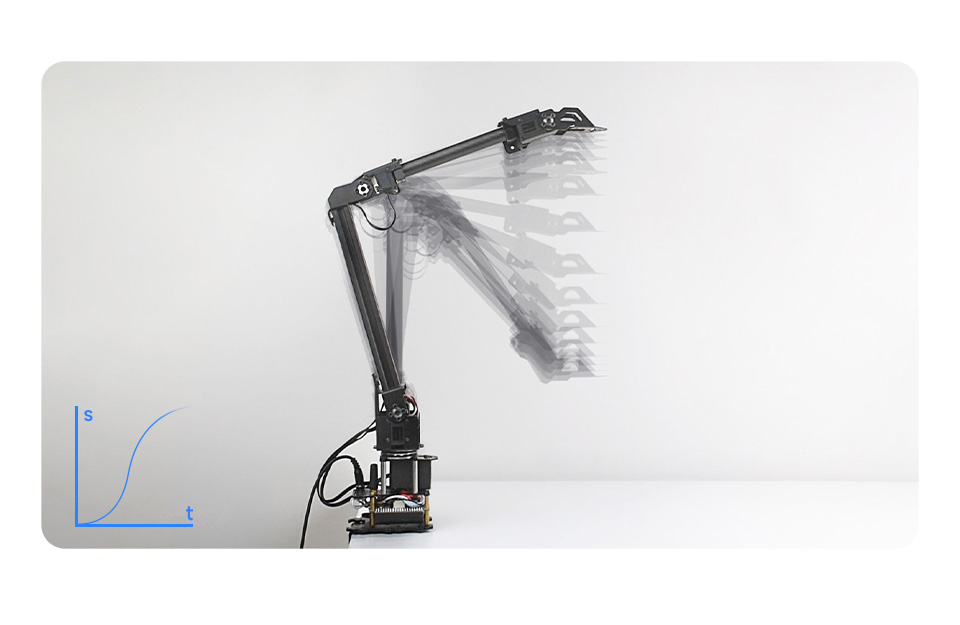
Low-delay remote collaboration

ESP-NOW is a low-delay ad hoc wireless communication protocol, without the need of Network infrastructures. You can use one robotic arm to wirelessly control other robotic arms, and the control methods can be set as broadcast control, group control, and one-to-one control.
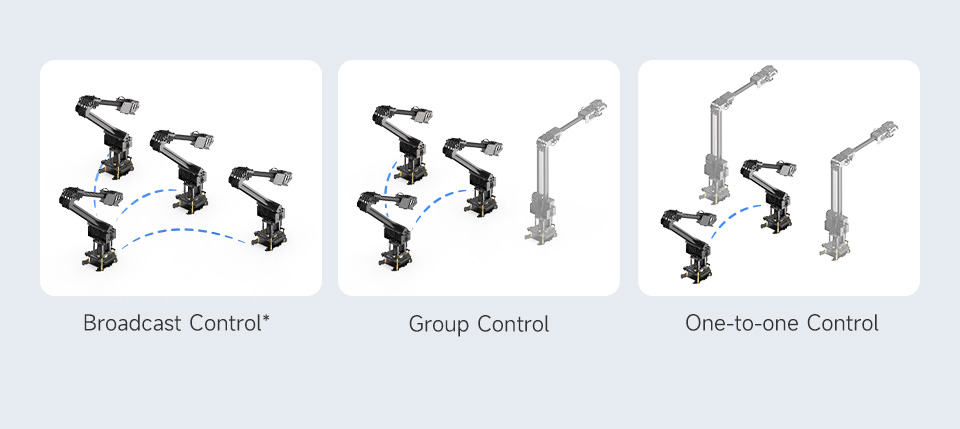
* Note: The broadcast control has no limitation for the number of controlled devices, while the group control allows up to 20 devices. Please refer to the WIKI for more details.

In the Leading-following control mode, the Leader robotic arm will send its joint angle information to other robotic arms via ESP-NOW communication. The other robotic arms which are in ESP-NOW Follower mode will imitate the same actions as the Leader in real time.
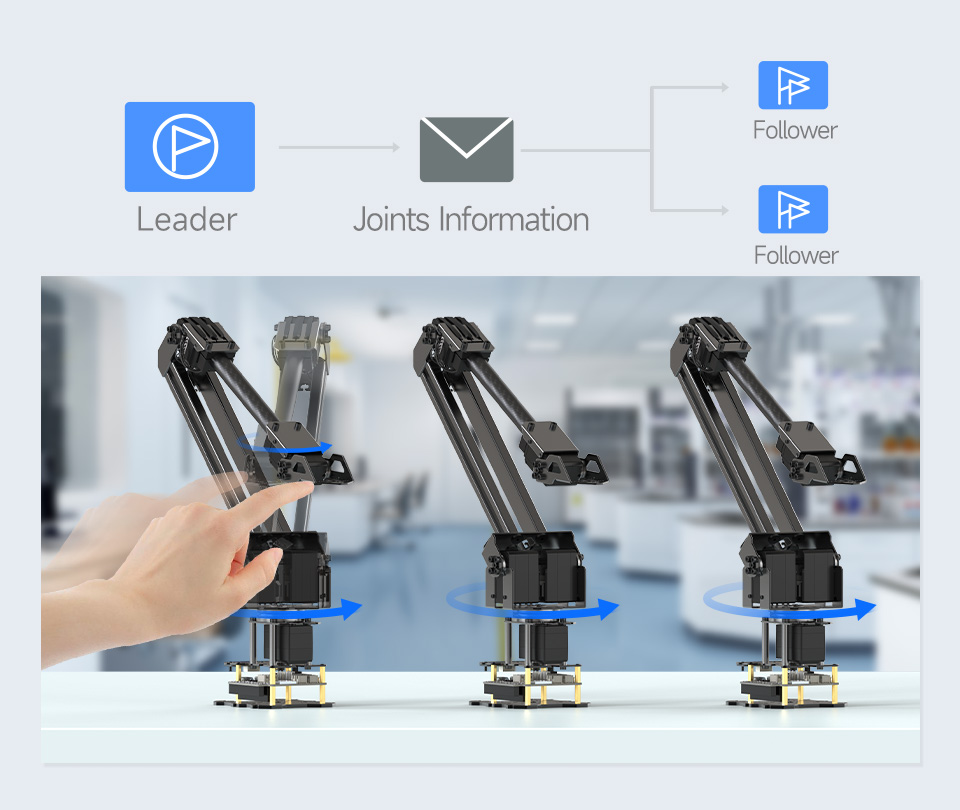
multiple devices and languages Support

RoArm-M2 series can be controlled not only by the WEB application, but also supports using other controllers to send JSON commands via HTTP protocol network request, serial communication, or USB communication for controlling and obtaining feedback.
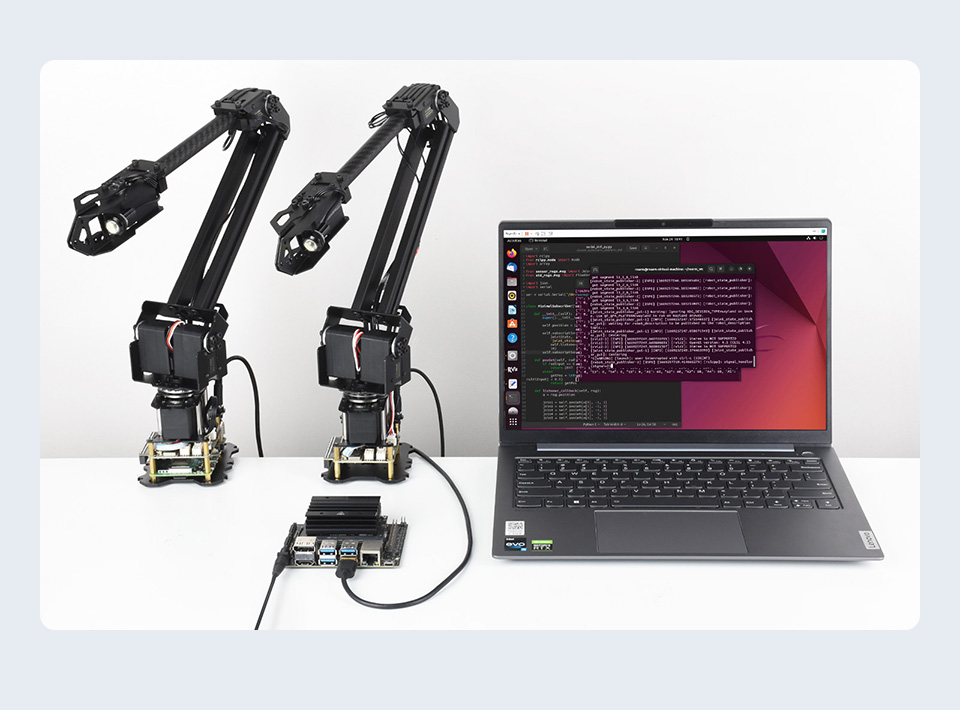

Provides multiple installation schemes and related secondary development resources, suitable for different usage scenarios and can be flexibly integrated into your projects and applications
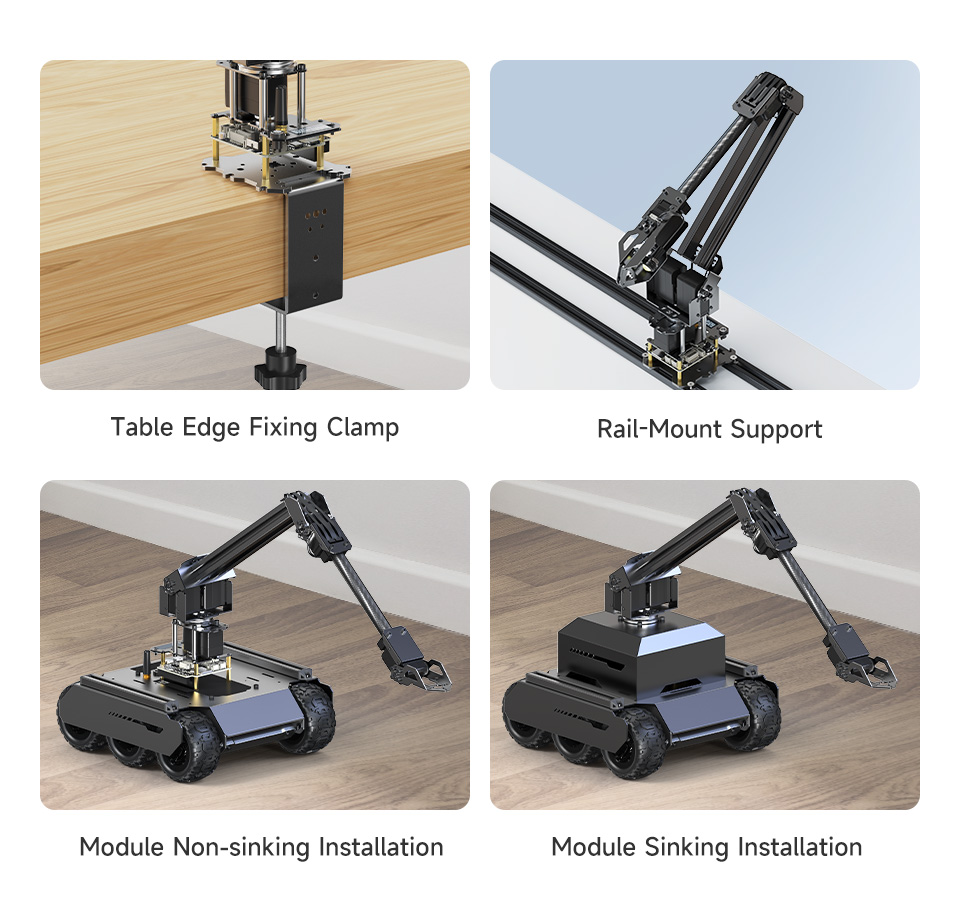

The main structure of the upper arm adopts two 1020 European standard aluminum rails, supports installing additional peripherals via the boat nuts to meet different needs. Comes with boat nuts and corresponding M4 screws for easy installation.
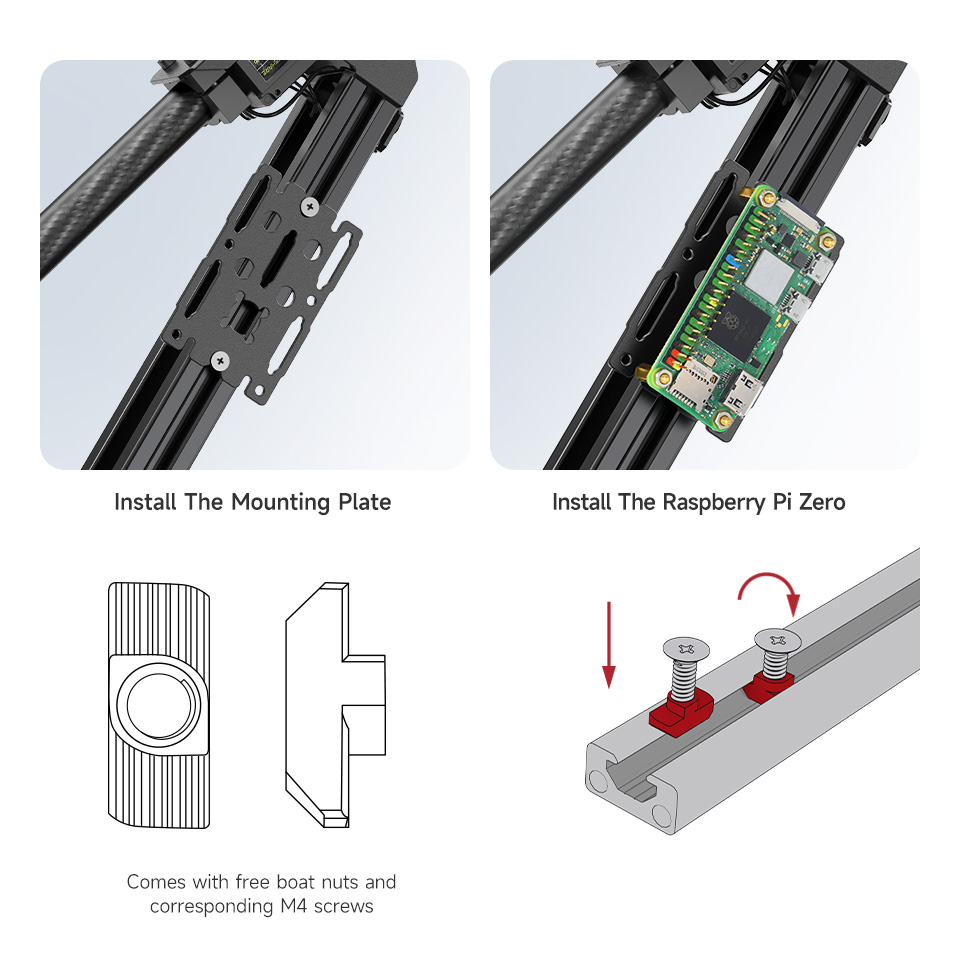
to extend visual applications

Comes with a camera holder and open source for the related drawings.
You can directly install a camera with the corresponding size or other cameras
with an adapter
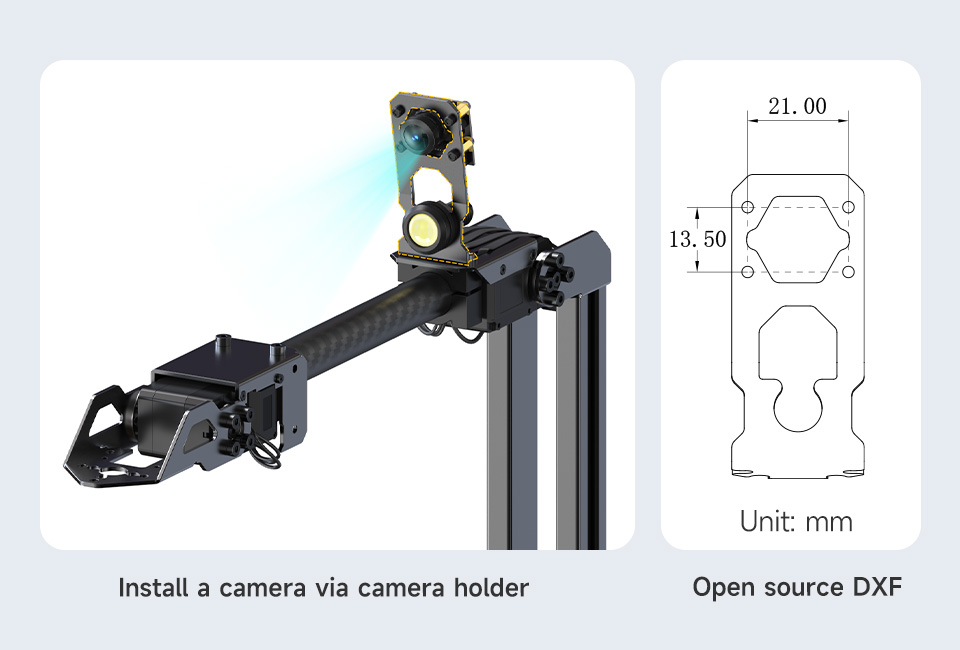
for more functions

Comes with an expansion plate, easy for users to expand and replace different EoAT
for more functions
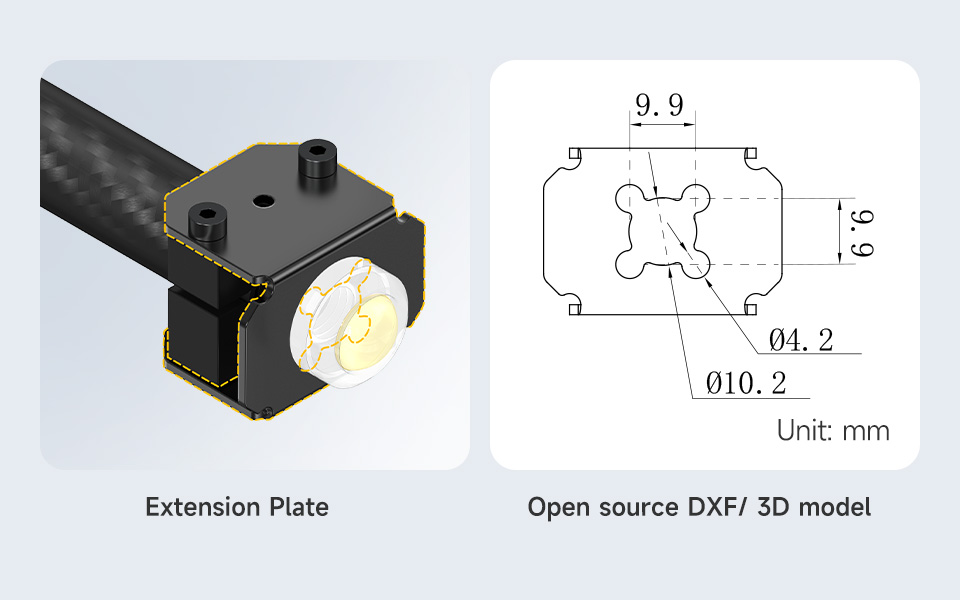

Adopts ESP32 powerful main control MCU, supports Multiple wireless communication protocols, with a large amount of open source resources to help secondary development of innovative applications
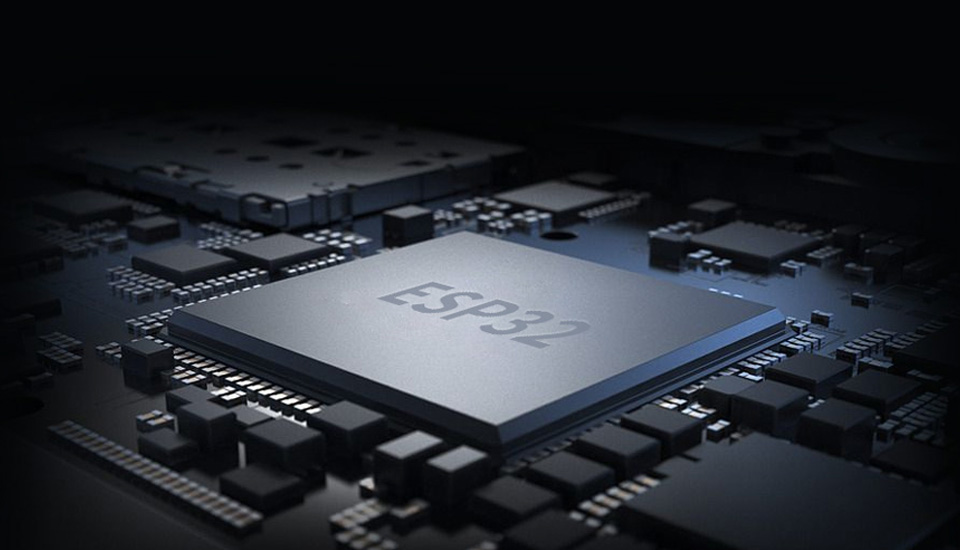
model establishment File and supports
multi-device cooperation

Provides communication nodes of ROS2, URDF model description file and zero-based tutorial of ROS2
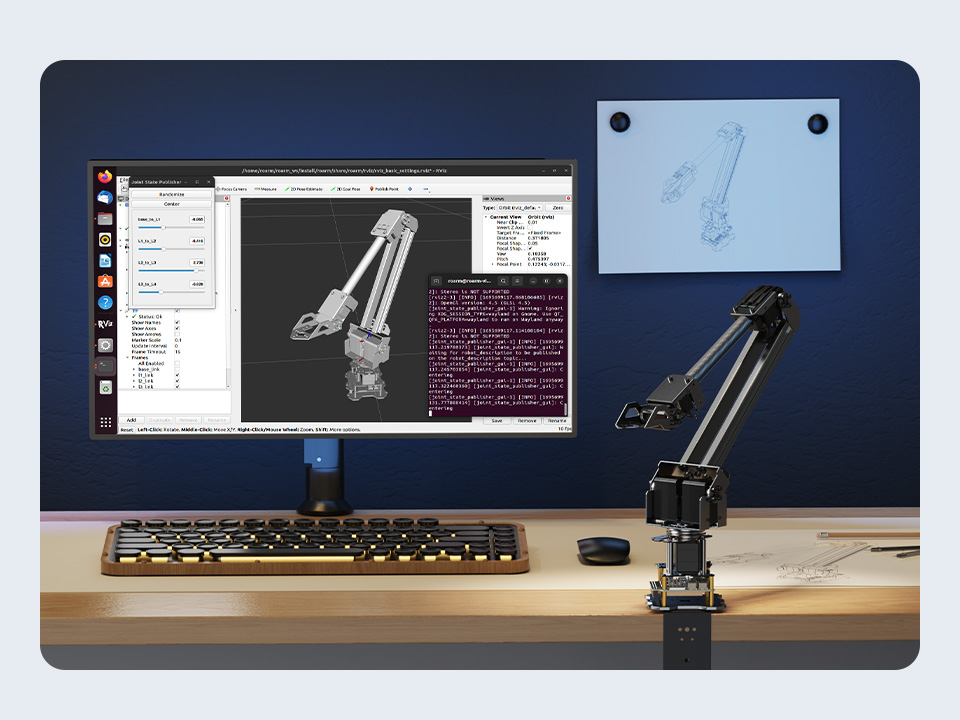
secondary development

We provide complete unit tutorials and cases, including various functions and common application scenarios, to help users get started quickly for secondary development
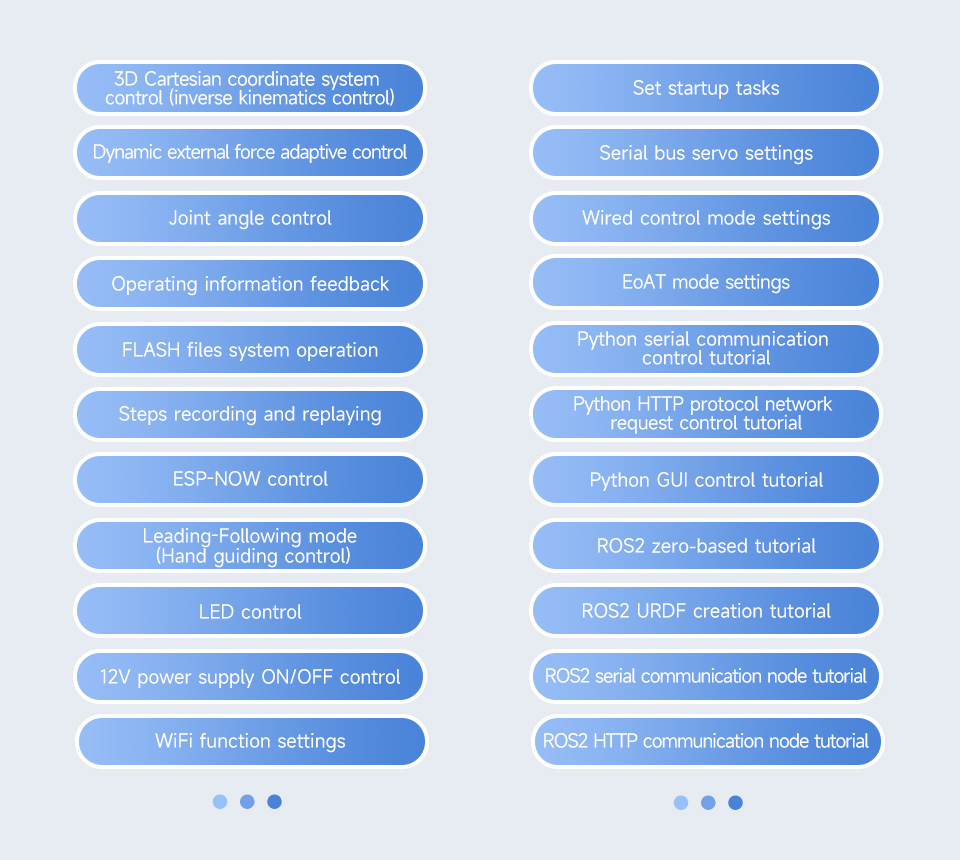

Onboard rich interfaces and resources for innovative development and functional expansion
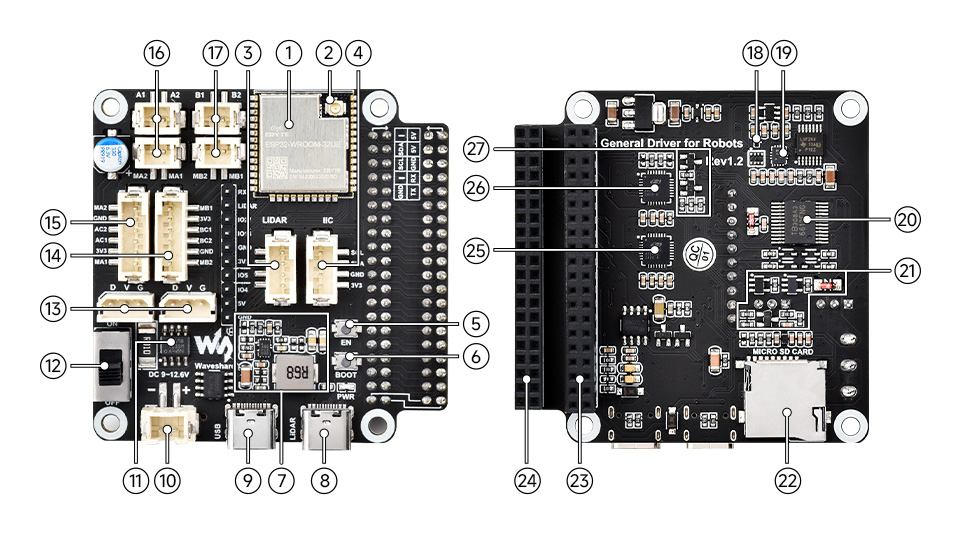
- ESP32-WROOM-32 controller module
Can be developed using Arduino IDE - IPEX1 WIFI connector
For connecting WIFI antenna to increase the wireless communication distance - LIDAR interface
Integrated radar adapter function - I2C peripheral expansion interface
For connecting with OLED screen or other I2C sensors - Reset Button
Press and release to reboot the ESP32 - Download button
The ESP32 will enter the download mode after powering on - DC-DC 5V voltage regulator circuit
Power supply for host computers such as Raspberry Pi or Jetson nano - Type-C port (LADAR)
LIDAR data transmission - Type-C port (USB)
ESP32 communication interface, for uploading programs to ESP32 - XH2.54 power port
Support DC 7~13V input, can directly power the serial bus servos and motors - INA219
voltage/current monitoring chip - Power ON/OFF
External power supply ON/OFF - ST3215 serial bus servo interface
For connecting with ST3215 serial bus servo - Motor interface PH2.0 6P
Group B interface for motor with encoder
- Motor interface PH2.0 6P
Group A interface for motor with encoder - Motor interface PH2.0 2P
Group A interface for motor without encoder - Motor interface PH2.0 2P
Group B interface for motor without encoder - AK09918C
3-axis electronic compass - QMI8658C
6-axis motion sensor - TB6612FNG
Motor Control Chip - Serial bus servo control circuit
for controlling multiple ST3215 serial bus servos and obtaining servos feedback - TF card slot
Can be used to store logs or WIFI configurations - 40PIN GPIO header
For connecting with Raspberry Pi or other host boards - 40PIN extended header
Easy to use the GPIO pins of Raspberry Pi or other host boards - CP-2102
UART to USB, for radar data transmission - CP-2102
UART to USB, for ESP32 communication - Automatic download circuit
For Uploading programs to the ESP32 without pressing the EN and BOOT buttons
Supports function expansion

Integrated TB6612FNG motor drive IC, INA219 battery voltage Monitoring, and 9-axis
IMU sensor, supports function expansion and innovation
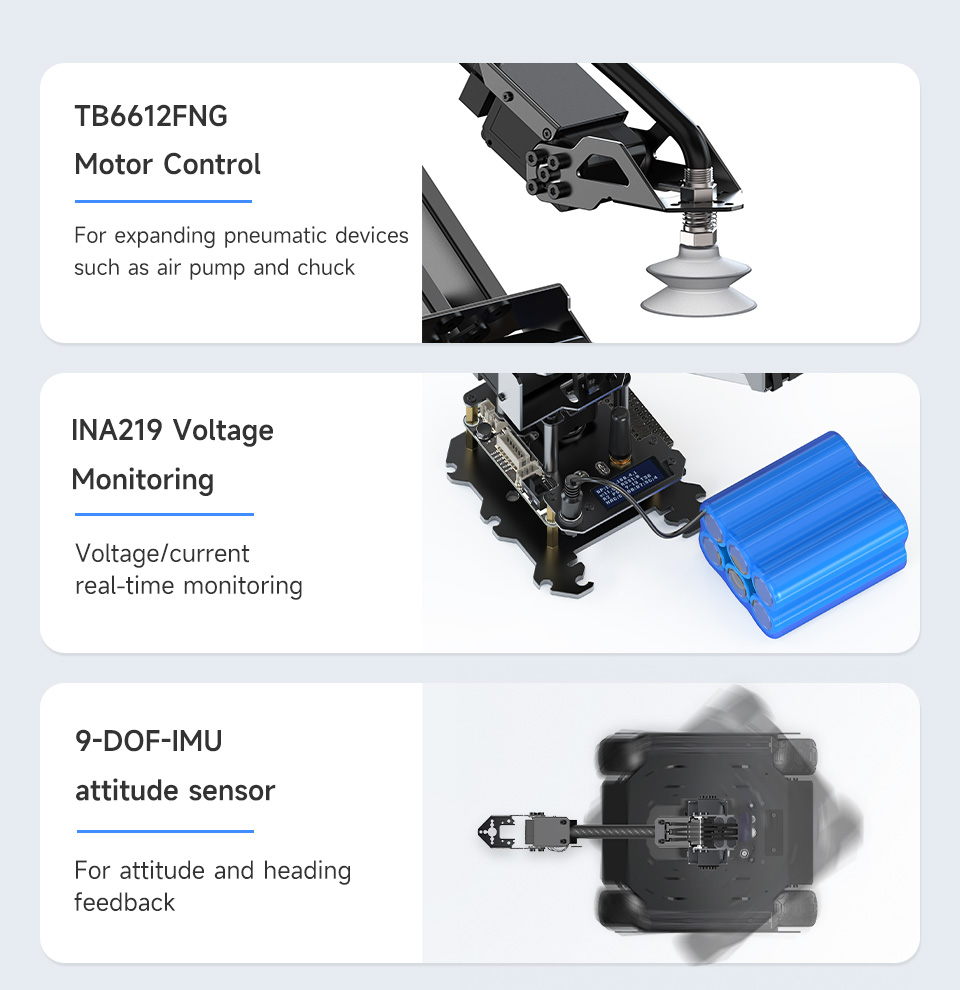
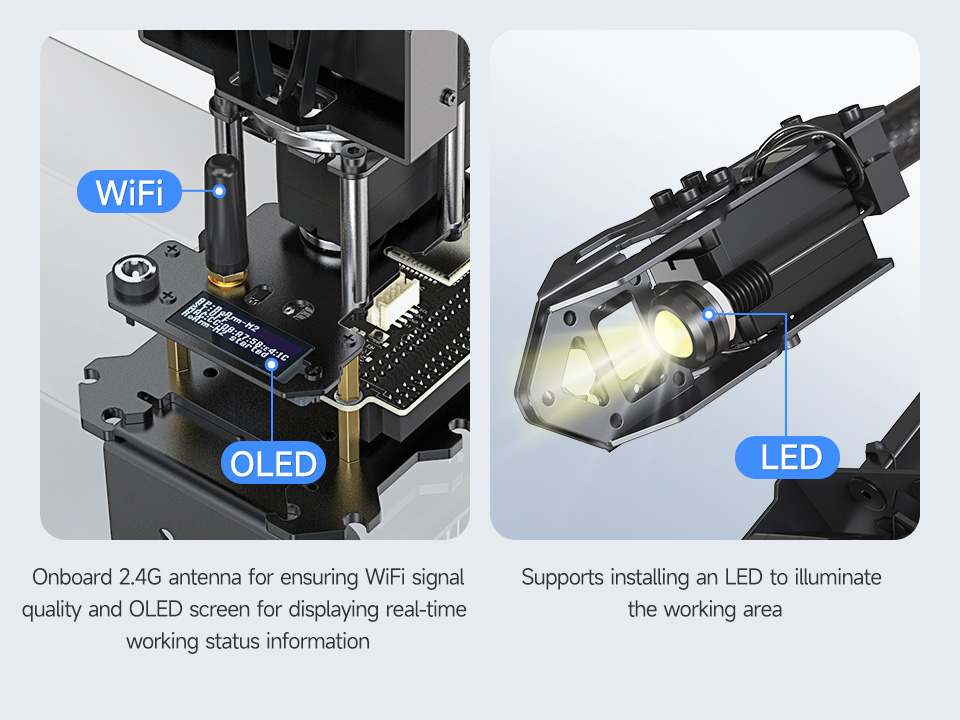

Provides Web applications and desktop software (open-source programs developed by Python), supports setting action instructions when the mouse is pressed and released
to control the robotic arm flexibly
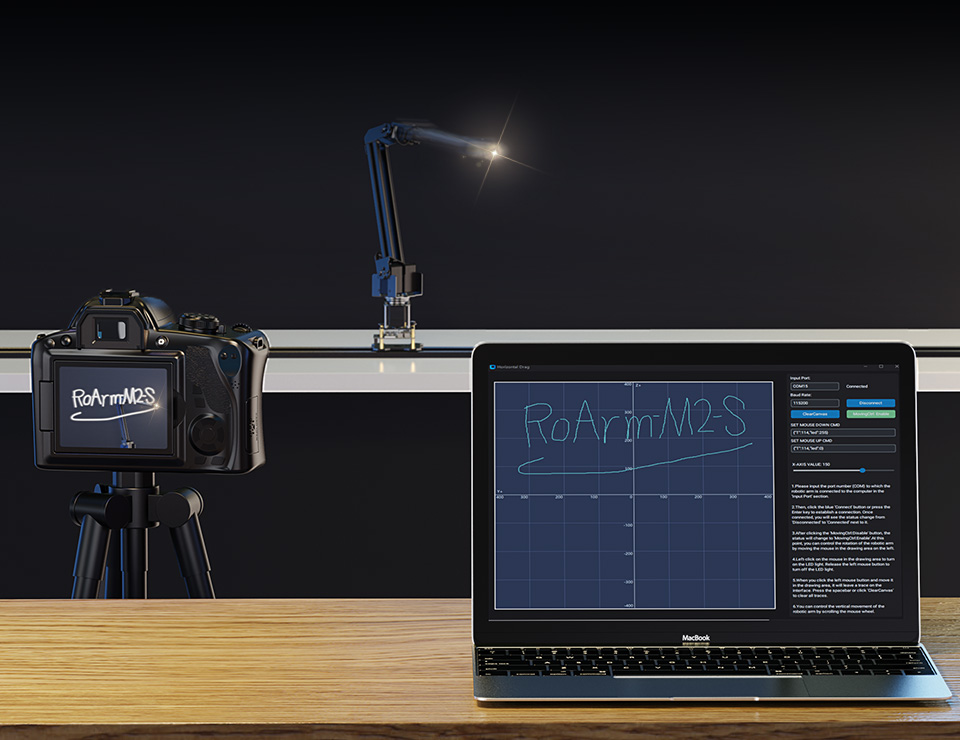
DOF | 4 |
---|---|
Work space | Horizontal diameter: 1090mm (Max, 360° omnidirectional), Vertical: 798mm (Max) |
Operating voltage | 12V 5A power supply, supports 3S Lithium batteries (NOT included) |
Load capacity | [email protected] |
repositioning precision | ≈±4mm (under the same load) |
Servo rotation speed | 40rpm (no-load, no torque limit) |
Operating range | BASE-360°, SHOULDER-180°, ELBOW-180°, HAND-135°/270° |
Drive type | TTL Serial bus servo, direct-drive joint |
Servo numbers | 5 |
Joint angle sensor | 12-bit 360° magnetic encoder |
Servo torque | 30KG.CM @12V |
Joint feedback information | servo status, joint angle, rotation speed, joint load, servo voltage, servo current, servo temperature and servo working mode |
Main control | ESP32-WROOM-32 |
Main control module features | WiFi, BT, Dual Core, 240MHz |
Wireless control mode | 2.4G-WiFi, ESP-NOW |
Wired control mode | USB, UART |
Manual operation mode | WEB control interface |
Host operation mode | UART/USB/ESP-NOW*/HTTP communication via JSON data format commands (* it does not support obtaining feedback information if using ESP-NOW communication) |
Host support | USB connection devices including Raspberry Pi, Jetson Orin Nano, and PC. |
EoAT function | clamp function by default, can be changed as an additional degree of freedom |
LED power | ≤1.5W |
OLED screen size | 0.91inch |
Other functions | 2-ch 12V power supply switch, 9-DOF IMU |
Robotic arm weight | RoArm-M2-S: 826 ±15g RoArm-M2-Pro: 873.3 ±15g (not including the table edge fixing clamp) |
table edge fixing clamp weight | 290g ±10g |
Supported table edge thickness of the clamp | <72mm |
Demo | 3D Cartesian coordinate system control (inverse kinematics control); Dynamic external force adaptive control; Joint angle control; Operating information feedback; FLASH files system operation; Steps recording and replaying; ESP-NOW control; Leading-Following mode (Hand guiding control); LED control; 12V power supply ON/OFF control; WiFi function settings; Set startup tasks; Serial bus servo settings; Feedback mode setting; EoAT mode setting, etc. (Note: Please refer to the WIKI for more details) |
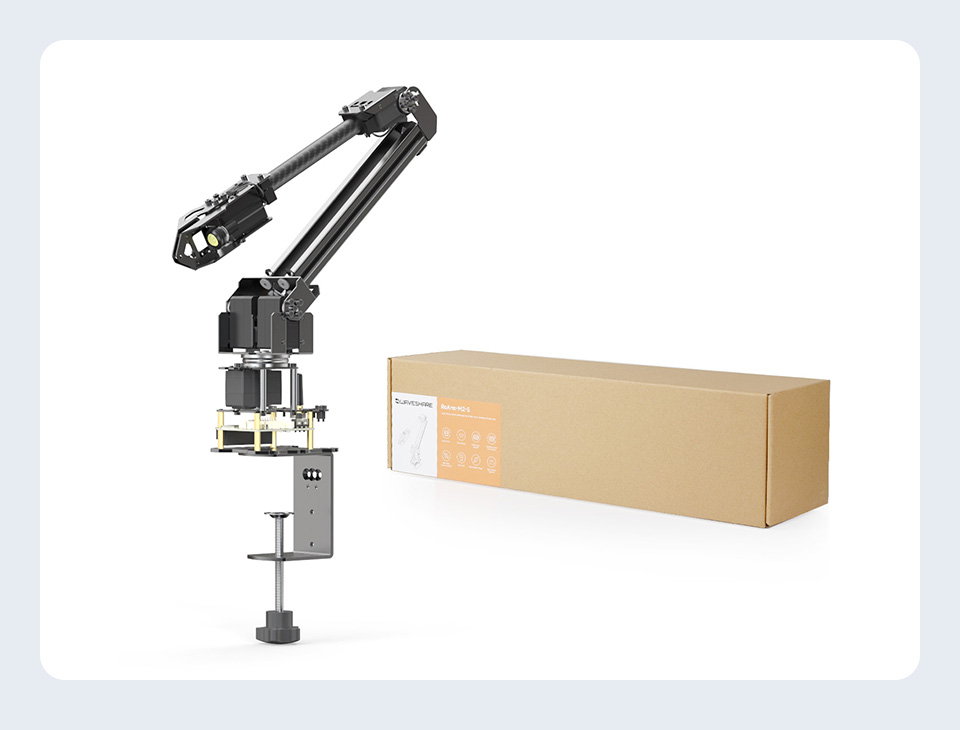
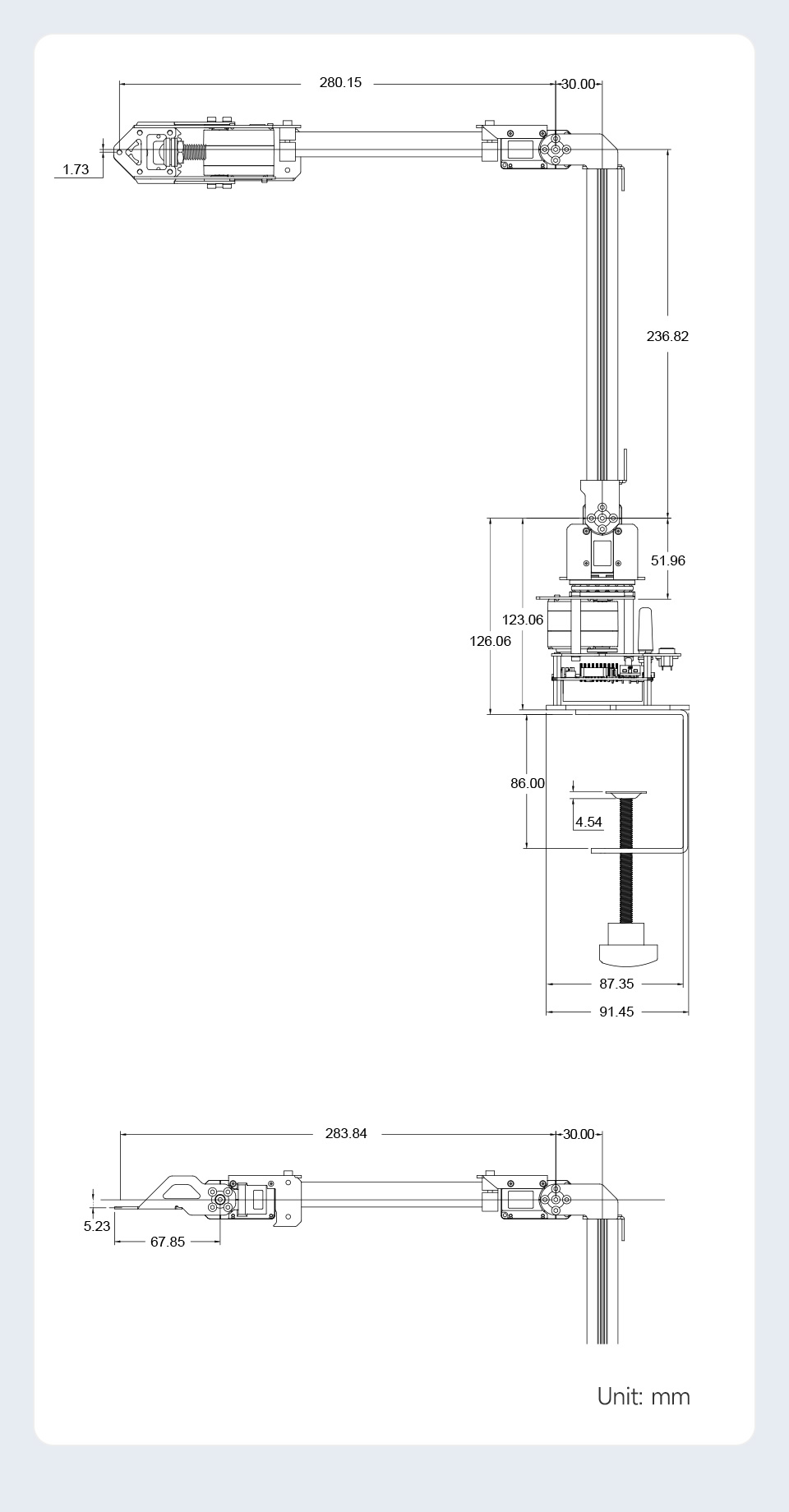

* Resources for different product may vary, please check the wiki page to confirm the actually provided resources.
Quick Overview
RoArm-M2-S
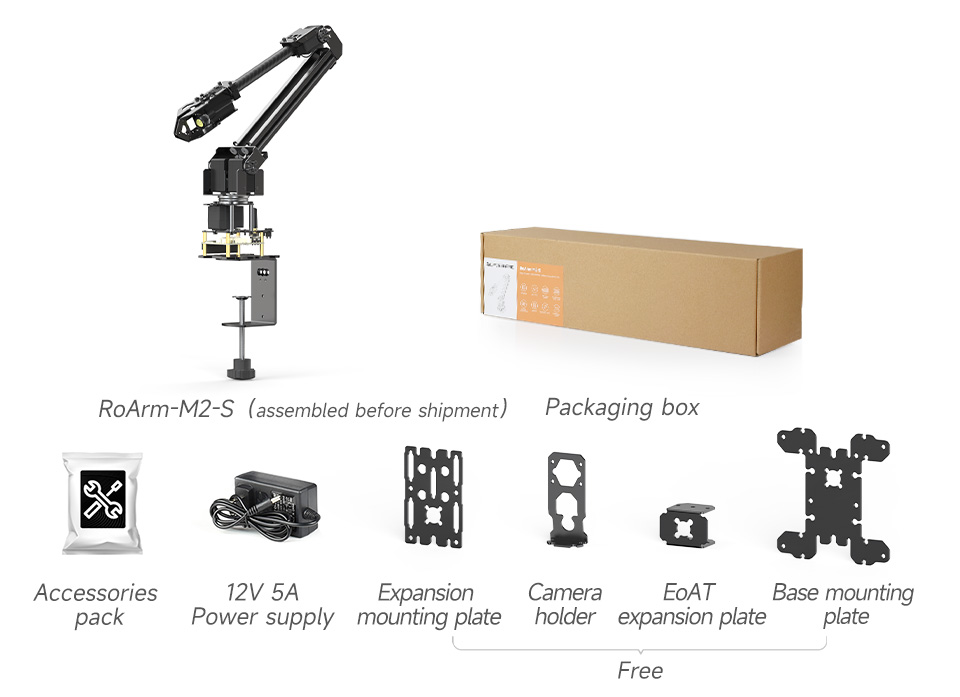
RoArm-M2-Pro
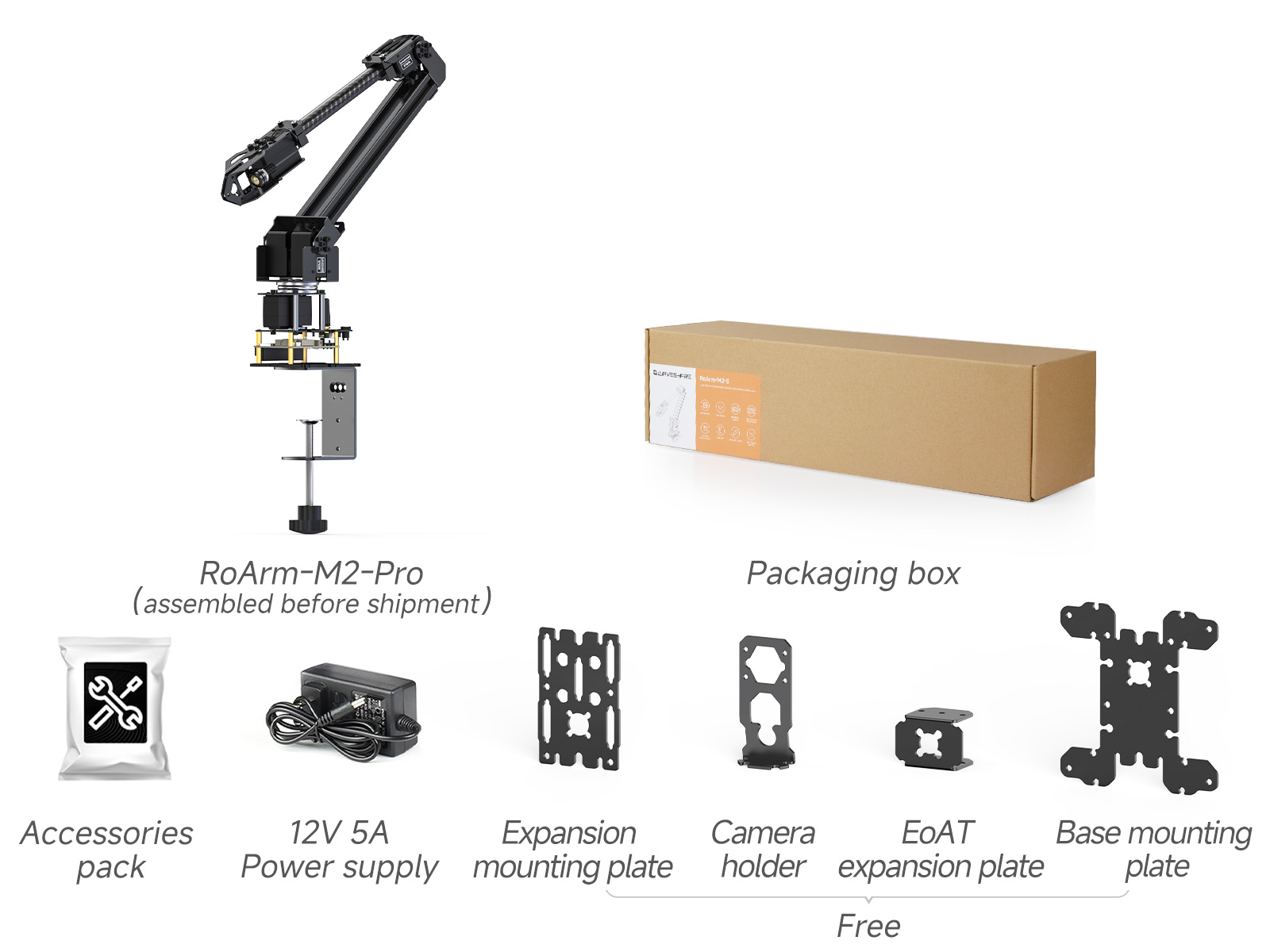